- Solutions
ENTERPRISE SOLUTIONS
Infuse new product development with real-time intelligenceEnable the continuous optimization of direct materials sourcingOptimize quote responses to increase margins.DIGITAL CUSTOMER ENGAGEMENT
Drive your procurement strategy with predictive commodity forecasts.Gain visibility into design and sourcing activity on a global scale.Reach a worldwide network of electronics industry professionals.SOLUTIONS FOR
Smarter decisions start with a better BOMRethink your approach to strategic sourcingExecute powerful strategies faster than ever - Industries
Compare your last six months of component costs to market and contracted pricing.
- Platform
- Why Supplyframe
- Resources
The global supply chain is an intricate, and occasionally delicate, network of interconnected customers and suppliers. Sourcing the components for a new product launch and maintaining an up-to-date bill of materials is difficult enough. But for the last two years, companies have been doing their best to introduce new products in a marketplace defined Covid-19’s extreme shortages.
Sounds almost impossible, right?
And yet, the wheels of commerce continue to turn. We at Supplyframe were curious what it was like to launch a new product during a pandemic. What unforeseen NPI challenges popped up? Were there opportunities for innovation or digital transformation within them? So we did what we do in these situations and commissioned a survey.
About The Study
The Supplyframe NPI (New Product Introduction) Sourcing Study talked to 251 companies in the global electronics value chain about the challenges they are facing as they create a bill of materials and ultimately bring their products to market.
The vast majority of respondents work in these fields:
- Computer Systems 34%
- Industrial Equipment and Heavy Machinery 33%
- Automotive and Mobility 24%
- Consumer Electronics 22%
- Telecom/Networks 22%
- Aviation, Aerospace, Defense 18%
- Medical Devices 16%
Respondents answered a series of questions, and the results will be presented here in a series of posts. As always we’ll try and offer solutions as well as laying out the issues.
Let’s Begin With The BOM
The first question we asked was in relation to the bill of materials (BOM). An accurate and up to date BOM is essential for successful product launches. But what our survey told us is that keeping them up to date with the most accurate and correct information is a challenge for the majority of businesses out there.
We asked respondents how frequently the following issues occurred in their company.
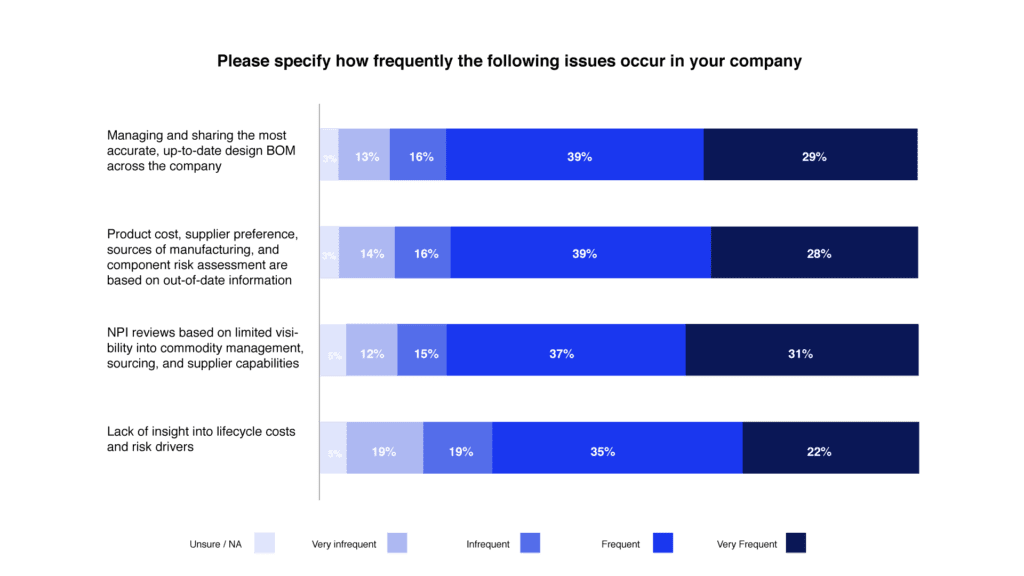
As you can see, more than half of the companies surveyed have frequent or very frequent issues with their BOMs. Let’s make our way through the list for a little more insight.
Issue #1: Managing and sharing the most accurate and up-to-date design BOM across the company.
Keeping things accurate and up to date is difficult, and essential. A small mistake or oversight on a bill of materials can create millions of dollars in lost time, rework, or incorrectly build products.
Every time a BOM is manually updated and re-shared throughout the organization it creates the chance for error. If you think about the staggering number of updates a design BOM undergoes before the product is complete, you start to see the importance of 100% accuracy. In today’s fast moving world, a BOM that reflects new intelligence in real time is a must.
Issue #2: Product cost, supplier preference, sources of manufacturing, and component risk assessment are based on out-of-date information.
67% of firms who answered our survey had this issue. So nearly 7 out of 10 businesses are basing their BOM on incorrect or outdated information. Pre-pandemic this would have been a big problem, but given the current constraints on the component market and ongoing shortages, an out of date BOM can be positively disastrous.
It’s worth taking a look at the categories here as well, because each one is its own world of particular volatilities and complexities.
- Product Cost: Stable costs rely on stable supply, and the supply of almost anything, especially high-demand components like semiconductors, is “alarmingly” unstable at the moment. Add inflation into the mix and you’ve got a recipe for off-the-wall unpredictability in pricing.
- Supplier Preference: Multi-sourcing vital components is an absolute necessity. Visibility is your friend in this regard, and relying on old ways won’t cut it in a very competitive market.
- Source of Manufacturing: Fingers crossed, it looks like the absolute worst of the Covid-19 pandemic is behind us, especially in terms of large scale factory closings. But count on floods, fires, and earthquakes, and countless other scenarios to do their share of damage.
- Component Risk Assessment: An overall metric of how likely it is something is going to go awry during the procurement process, if this is made with outdated or incorrect information from 1-3 above, it’s not going to be accurate.
Issue #3: NPI reviews based on limited visibility into commodity management, sourcing, and supplier capabilities.
While the scale varies from business to business, a new product or component introduction is expensive. It’s capital that could be invested elsewhere. The market could shift and your product is no longer relevant. However you look at it, it’s a risk. 68% of the businesses we talked to said it happens frequently or very frequently.
Any lack of visibility represents a threat to the success of your NPI. Acting on incorrect or outdated information can set a project back weeks or months. Firms that will succeed in this challenging time for the market will have superior market intelligence in their corner.
Issue #4: Lack of insight into lifecycle costs and risk drivers.
Over half the organizations we talked to expressed frustration with figuring out the most cost-effective way of executing a new product introduction. It relies on first rate market intelligence and excellent visibility up and down your supply chain.
The risks a business faces during the process go far beyond internal delays or a mis-shipped component. As we mentioned above, natural disasters are a constant threat and can bring production to a halt instantly in critical manufacturing sectors. Developments in technology may put your product at a disadvantage before it’s ready for market.
Understanding your product’s path towards a successful launch means giving yourself a holistic view of the risks you face and the ability to capitalize on them if possible, and turn them into advantages.
How Supplyframe Reinvents NPI
We have a vision of a more resilient way to introduce new products. One that starts with collaboration and uses automation and AI to update the BOM in real time for a continually evolving picture of your risk. One that searches out and suggests alternate components as needed.
Supplyframe NPI is a solution that impacts every step of the traditional product lifecycle to enhance margins, help create a single version of truth, and ensure supply continuity, directly addressing NPI challenges in 2022 and beyond.