- Solutions
ENTERPRISE SOLUTIONS
Infuse new product development with real-time intelligenceEnable the continuous optimization of direct materials sourcingOptimize quote responses to increase margins.DIGITAL CUSTOMER ENGAGEMENT
Drive your procurement strategy with predictive commodity forecasts.Gain visibility into design and sourcing activity on a global scale.Reach a worldwide network of electronics industry professionals.SOLUTIONS FOR
Smarter decisions start with a better BOMRethink your approach to strategic sourcingExecute powerful strategies faster than ever - Industries
Compare your last six months of component costs to market and contracted pricing.
- Platform
- Why Supplyframe
- Resources
The Fifth Industrial Revolution, AKA Industry 5.0, has arrived on the factory floor. It is characterized by a higher level of digital interconnectedness within the smart factor compared to Industry 4.0. One important addition to Industry 5.0 is a focus on sustainable innovation and human-centricity, which will complement Industry 4.0. Together, they will become the new dominant model for manufacturing operations in the years ahead.
Industry 4.0 was introduced in 2011 and has been the primary model for industrial manufacturing operations for over a decade. Industry 4.0 introduced several technologies that have significantly impacted supply chain management. They include the Internet of Things (IoT), intelligent automation, big data analytics, artificial intelligence (AI), and advanced robotics. At the same time, Industry 4.0 removed humans from the shop floor. Industry 5.0 will further these advancements.
Of course, Industry 4.0 is not being retired. It will complement Industry 5.0 to make further advances and create a more holistic approach that emphasizes human-machine collaboration, customization, and a commitment to environmental sustainability.
Sustainability is especially important in resource- and energy-intensive industries, such as mining and industrial manufacturing. Businesses focused on sustainability will be more attractive to potential investors, employees, and customers. The adoption of Industry 5.0 will promote the economic performance of industries while ensuring environmental sustainability.
Where Industry 4.0 placed smart technologies at the center of manufacturing operations and across the supply chain, Industry 5.0 is reintroducing humans to the factory floor alongside robots, machinery, and digital ecosystems. In addition, it includes environmental sustainability. The partnership between humans and smart machines marries the accuracy and speed of industrial automation that never gets tired with the creativity, innovation, and critical thinking skills of humans.
Here’s how Industry 5.0 and Industry 4.0 might impact supply chain management.
1. Human-Machine Collaboration. Industry 5.0 envisions a future where humans and robots work side-by-side on the factory floor. This collaborative approach will lead to better forecasting and risk management and allow for adaptive responses to disruptions.
2. Customization and Personalization: Industry 5.0 will focus on mass customization of products, allowing manufacturers to produce tailored products at scale. This can affect supply chains by requiring more flexible production processes and agile supply networks capable of responding to individual customer demands.
3. Decentralized Production and Local Sourcing: Industry 5.0 will likely encourage the decentralization of production, with smaller production units closer to end markets. This approach could lead to shorter supply chains, reduced transportation costs, and potentially more sustainable operations.
4. Sustainability and Green Supply Chains: As sustainability becomes a corporate concern, companies will integrate eco-friendly practices across the supply chain. This will involve using AI and data analytics to optimize energy consumption, reduce waste, and minimize environmental impacts.
5. Real-time Data Sharing: Industry 5.0 might promote real-time data sharing across the supply chain, enabling better visibility and transparency. This could enhance collaboration, minimize delays, and improve overall efficiency.
6. Cybersecurity and Data Privacy: With increased connectivity comes the need for enhanced cybersecurity and data privacy measures. Industry 5.0 would likely require robust security protocols to protect sensitive supply chain data from cyber threats.
7. Resilience and Risk Management: Industry 5.0 will place a greater emphasis on building resilient supply chains that rapidly adapt to disruptions, such as pandemics, geopolitical events, and natural disasters. This might involve strategies like dual sourcing and scenario planning.
8. Talent Development: As Industry 5.0 blurs the lines between human and machine work, workforce development becomes crucial. Supply chain professionals must acquire new skills to manage advanced technologies effectively.
Source: The Impact of Industry 5.0 on Supply Chain Management
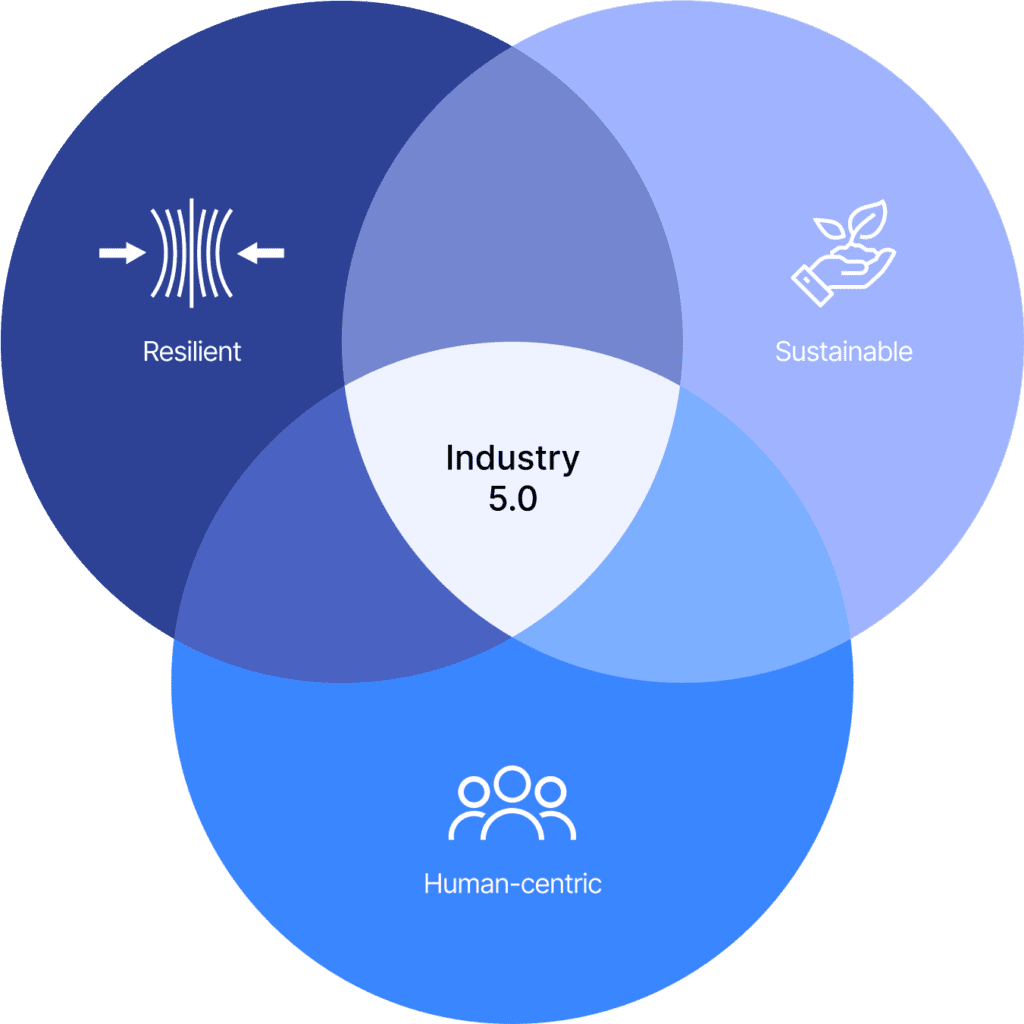
These are just a few examples of how Industry 5.0 will be used in supply chain management. As the technologies mature, there are likely to be more innovative ways to manage supply chains. Other issues include the cost of Industry 5.0 technologies, concerns about data security, and the shortage of skilled workers who can install and manage Industry 5.0.
The challenges include the higher cost of Industry 5.0 compared to Industry 4.0. Also, an increase in the data required in Industry 5.0 will require higher levels of data security. Also, many companies can expect a steep learning curve for new workers to gain the expertise necessary to implement Industry 5.0. As a consequence, the workforce could be resistant to adopting new technologies.
Regardless of these challenges, the potential benefits of Industry 5.0 for supply chain management are expected to be significant. The combination of new technologies, the integration of humans, and a commitment to environmental sustainability will be at the center of industrial processes. In addition, implementing Industry 5.0 technologies is likely to provide a competitive advantage and improve the bottom line.
The Supplyframe Advantage
The foundation of Industry 5.0 is built on a human-centric foundation together with manufacturing processes that align with environmental goals and resilience. It will bring a significant change to industrial manufacturing operations that will shape the future of manufacturing operations.
Supplyframe, a Siemens Company, has strong relationships with industrial manufacturers across a diversity of industries including Automotive, Aerospace and military, Industrial Equipment, Consumer Electronics, Mining, and other sectors. The company is ideally positioned to provide consulting services to these companies to implement the integration of Industry 5.0 capabilities.
Challenges implementing Industry 5.0
The very first industrial revolution dates back to the 1760s (Industry 1.0), when new manufacturing processes began to use novel ways of generating energy, specifically running water and steam. The continuous evolution of manufacturing technology over the centuries has resulted in today’s large-scale, highly complex manufacturing operations that produce output on an enormous scale.
Of course, there will be challenges companies will face in adopting Industry 5.0. The primary issue is the high cost of implementation and the shortage of skilled workers with the expertise to implement Industry 5.0. Another significant issue that needs to be addressed is data security.
The bottom line: Businesses implementing Industry 5.0 will gain a competitive advantage over the competition, which will translate in revenue and business growth.
Design-to-Source Intelligent Network
The Supplyframe DSI Network is our proprietary network of over 70 vertical search engines, community sites, and media properties Over 10 million engineering, sourcing, and supply chain professionals regularly engage with the Supplyframe network properties and SaaS solutions in the course of their daily research and decision-making.
Within the DSI Network, users access comprehensive, continuously updated information spanning a universe of over 1 billion in-market part attributes, including real-time availability and lead-time data, along with 700,000 downloadable 2D and 3D models.
Most importantly, user engagement within the DSI Network fuels billions of continuous signals relate to global electronics part supply, demand, risk factors, and commercial intent. This rapidly expanding data asset is the foundation for transformational intelligence.
Today, the DSI network serves 15 million engineering and sourcing professionals. It has 70+ vertical search engines, as well as community sites and media properties. One-billion-plus searchable part attributes and 600-plus million components.